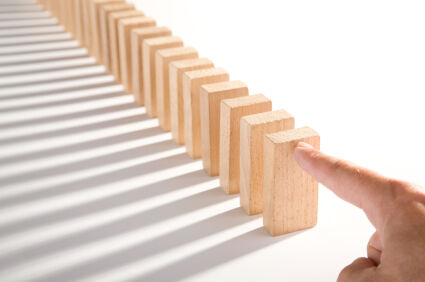
Successful organisations are made up of multiple teams across organisational levels creating an improvement leader network to drive up performance.
These internal networks exist in all organisations but their presence is typically so informal and pervasive that their potential is rarely recognised.
The Lean TPM Centre of Excellence process is a vehicle to develop this improvement leader community into linked, collaborative all star teams (rather than teams of all stars) by providing:
- Alignment on direction, where there is a shared belief about what the company is striving toward and the role of the team in getting there.
- High-quality interaction, characterised by trust, open communication, and a willingness to embrace conflict.
- An environment in which team members are energised because they feel they can achieve something that matters.
MILESTONE 1: PLANNING AND PREPARATION
The first step is an awareness and review session to raise understanding of Centre of Excellence Benchmark standards and assess current status against them. That includes a working sessions to agree barriers and gaps and identify action plans to build on existing capabilities.
Mobilisation involves a hands on workshop around up to three troublesome assets. During the workshop, a mix of Team Leaders, production and maintenance personnel apply the TPM Asset Improvement Plan to each asset to assess condition issues, gaps in best practice, improvement potential and an action plan to deliver that potential. That included the use of Lean thinking concepts to improve best practice standardisation, workflow and added value time.
At the end of the workshop, action plans are developed for a pilot programme to firm up on how to improve the asset and prevent a recurrence of the issues identified during the workshop.
MILESTONE 2: PILOT APPLICATION
During the pilot improvement leaders work together to raise their teams ability to use data, improve asset condition and adopt a focussed improvement agenda.
This involves launching small cross functional improvement teams to work on the issues identified during the workshop as a workplace learning project alongside their normal duties.
During the pilot programme, the teams apply the same TPM Asset Improvement Plan workbook briefing notes used during the mobilisation workshop to assess condition issues, gaps in best practice, improvement potential and take actions to deliver that potential. That includes the use of Lean thinking concepts to improve best practice standardisation, workflow and added value time.
Team Leaders are mentored by their managers and Internal Facilitators to
- Coach their teams through what they had learned in the TPM workshop.
- Capture the lessons learned as case studies and policy guidelines.
- Develop a practical roll out cascade to transfer those lessons to other areas.
ROLL OUT CASCADE
The blueprint for transferring the lessons learned from the pilot process to other areas will be developed as part of the pilot programme. Typically this will involve a phased approach to allow time to develop new capabilities and working relationships.
DELEGATE
As new ways of working improve effectiveness, asset care routines are simplified and can be transferred to front line teams to lock in the gains and release Engineer time to focus in process optimisation.
To unlock the potential of individuals and support the delivery of business goals, we can also create training programmes and in-house training academies to drive tangible performance improvement.
NEXT STEPS?
The first step is the awareness and review session to assess current status against the Lean Maintenance benchmarks. That includes working sessions to agree barriers and gaps and identify action plans to build on existing capabilities.
That supports the development of a mobilisation programme to launch the pilot phase of the Centre of Excellence programme. A Programmes that will:
- Encourage ownership of learning goals and pathways.
- Provide individuals and teams with the skills they need to deliver year on year improvement.
- Reinforce a proactive culture and the values of the organisation.
To find out more check out our support programme send us a message here or contact us via