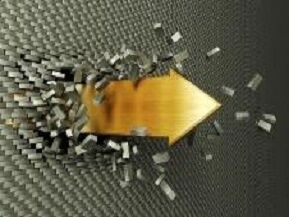
The LeanTPM Roadmap, developed over 30 years of practical application, provides an insight into how successful organisations deal with the multiple factors that interact to drive performance. Not just at any given moment but over months, years or even decades. Over that timescale, markets change, people move on, new people join, technology advances. Change is the only constant.
The Roadmap sets out a leadership agenda to guide long term progress against difficult to measure areas that underpin progress towards industry leading performance. That includes the impact of enablers such as the quality of learning and development, use of data, problem ownership and buy in to long term business goals.
At the heart of the LeanTPM Roadmap a journey to improve three areas of capability as set out below. (Click on the header links for more detail)
Centre of Excellence To Unlock The Full Potential
Organisations that successfully deliver lasting improvement, invest time in creating Centres of Excellence by developing workforce capability to prevent the causes of failure, eliminate waste and improve workflow as part of the daily routine.
That is well illustrated by the words of this CI manager after their programme began to deliver outstanding performance.
"In the beginning of the improvement journey, one of our top Production Managers thought, that 90 % of the reasons for ineffective use of the machinery was due to short term technical problems. Today he recognises that time invested in developing people to prevent problems is the route to high performance."
Lean Maintenance To Enhance Added Value
Lean Maintenance guides the development of Maintenance Team capability to support the evolution of the LeanTPM Centre of Excellence through actions to:
- Reduce recurring breakdowns and increase equipment effectiveness.
- Increase machine reliability, optimise maintenance schedules and release maintainer resource to undertake value adding engineering improvements.
- Balance Maintenance team skillsets and Predictive Maintenance capability
- Adopt data driven decision making through better use of CMMS systems and processes
- Establish a proactive continuous improvement "mind-set"
Technology Project Delivery Where People Matter
Every business needs to develop the capability to deliver projects well to respond to changes in market conditions and advances in technology. As almost all new ideas require testing to confirm proof of concept or to refine changes in work routines, Project Delivery is at the heart of any improvement process.
Unfortunately, studies show that only 1/3 of organisations achieve their planned level of return on investment. The most common pitfalls occur at the early stages including how investment choices are made and projects defined. This is compounded by project governance weaknesses and project risk management.
Connecting the dots around people plant and processes brings out the importance of people in the mix of levers that impact on the return on investment of technology projects. Research shows that where employees contribute to projects they are more than 3 times as successful as those that are purely driven top down.
Next steps?
The first step is a management awareness and review session to assess current status against the road map benchmarks. That includes a working sessions to agree barriers and gaps and identify action plans to build on existing capabilities.
That supports the development of a mobilisation programme to launch the pilot phase of the Roadmap programme
To find out more check out our support programme, send us a message here or contact us via